Replacing risers for Statoil/Reinertsen
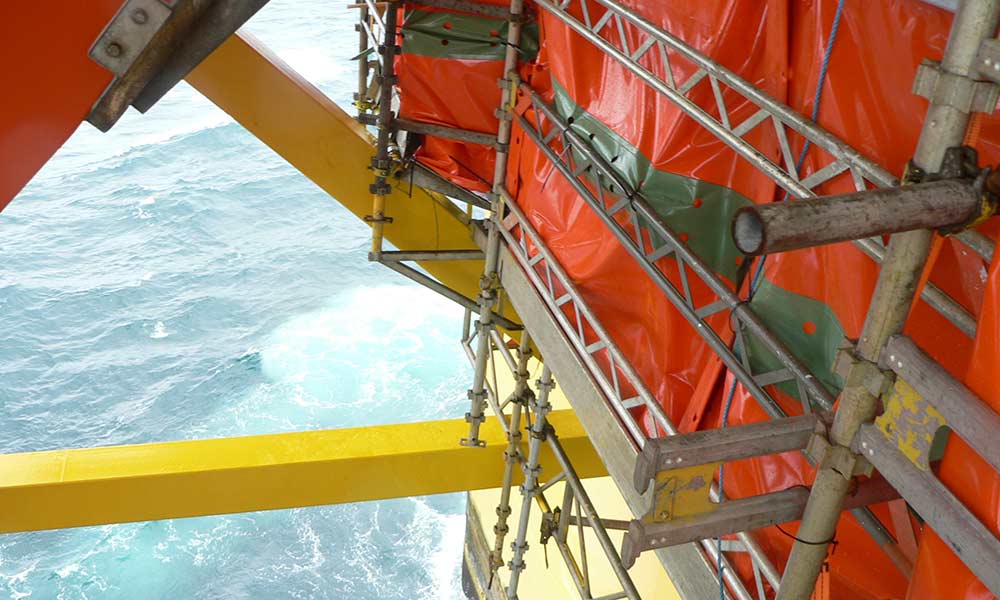
Troll is a natural gas and oil field in the Norwegian sector of the North Sea, one of the biggest in the North Sea, holding 40% of Norway’s gas – it also possesses significant quantities of oil, in thin zones under the gas cap, to the west of the field. The field as a whole consists of the main Troll East and Troll West structures in blocks 31/2, 31/3, 31/5 and 31/6, about 65 kilometres (40 mi) west of Kollsnes, near Bergen. Most of the gas lies in Troll East.
The field is operated by Statoil, which has a 30.58% interest. The other partners are Petoro (56%), Royal Dutch Shell (8.1%), ConocoPhillips (1.62%) and Total S.A. (3.69%).
The Troll B Platform is a semi-submersible designed by Doris and fabricated from concrete; thought to be the only concrete semisubmersible. This platform came into production in 1995.
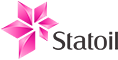
Reinertsen
2015 - 4 weeks
20 hours welding work
Two-person multidiscipline personnel for scaffolding, rigging and habitat
In accordance with plan
No accidents or incidents
Riser replacement E-test SLMP 2014 - 2017
Scope
The end-user, Statoil, needed to change out two production risers, while keeping production on the platform running. The main challenge we faced was to minimize the actual downtime, while staying in line with the Norwegian HSEQ governance, which prohibits more than one ignition source being present on the platform at the same time, therefore limiting the number of simultaneous welds that can be performed while the platform is producing.
Solution
We worked closely together in the project planning with both Statoil and the main contractor, Reinertsen. Our project managers were involved in both risk assessment, initial planning, choice of solution and in-field project management.
To solve the issue of simultaneous welding we decided to go for two separate habitats connected in series. With this solution, you have two independent habitats operating as one system and security barrier, with gas detection, loss of pressure and emergency stop on both systems working in tandem. This enabled us to perform the two welds simultaneously, while keeping safety at a maximum.
Result
Our tailored solution led to the contractor being able to perform both welds simultaneously, resulting in the job on the risers being completed five days ahead of schedule. Having both the risers back in full production five days ahead of schedule led to significant economical savings. The feedback from the customer was excellent, with both the project planning, technical solution and execution of the job being highlighted as exemplary.
No shutdown, no stress.
Leave your number or email and we’ll get in touch to discuss your next project.